Most sportswear and outdoor clothing is made, at least in part, from synthetic materials. These are mostly polyester, polyamides (or 'nylons'), and polyurethane (the base for elastane, a.k.a. Lycra, Spandex). Each material is traditionally synthesised from fossil fuels, which is a growing and serious concern for the clothing industry as a whole.
While most brands assert that the performance and durability of their synthetic materials outmatch natural alternatives — an argument with some validity — we're starting to suspect that much more can be done achieve a lighter environmental footprint without compromising the quality of their clothing.
A prime example is UYN, an exciting new(ish) Italian brand founded in 2018 under Trerè Innovation. Both Trerè and UYN (which stands for 'Unleash Your Nature' and is pronounced – get this – "win") are hell-bent on creating top-of-the-line outdoor clothing and sportswear without any materials made from fossil fuels.
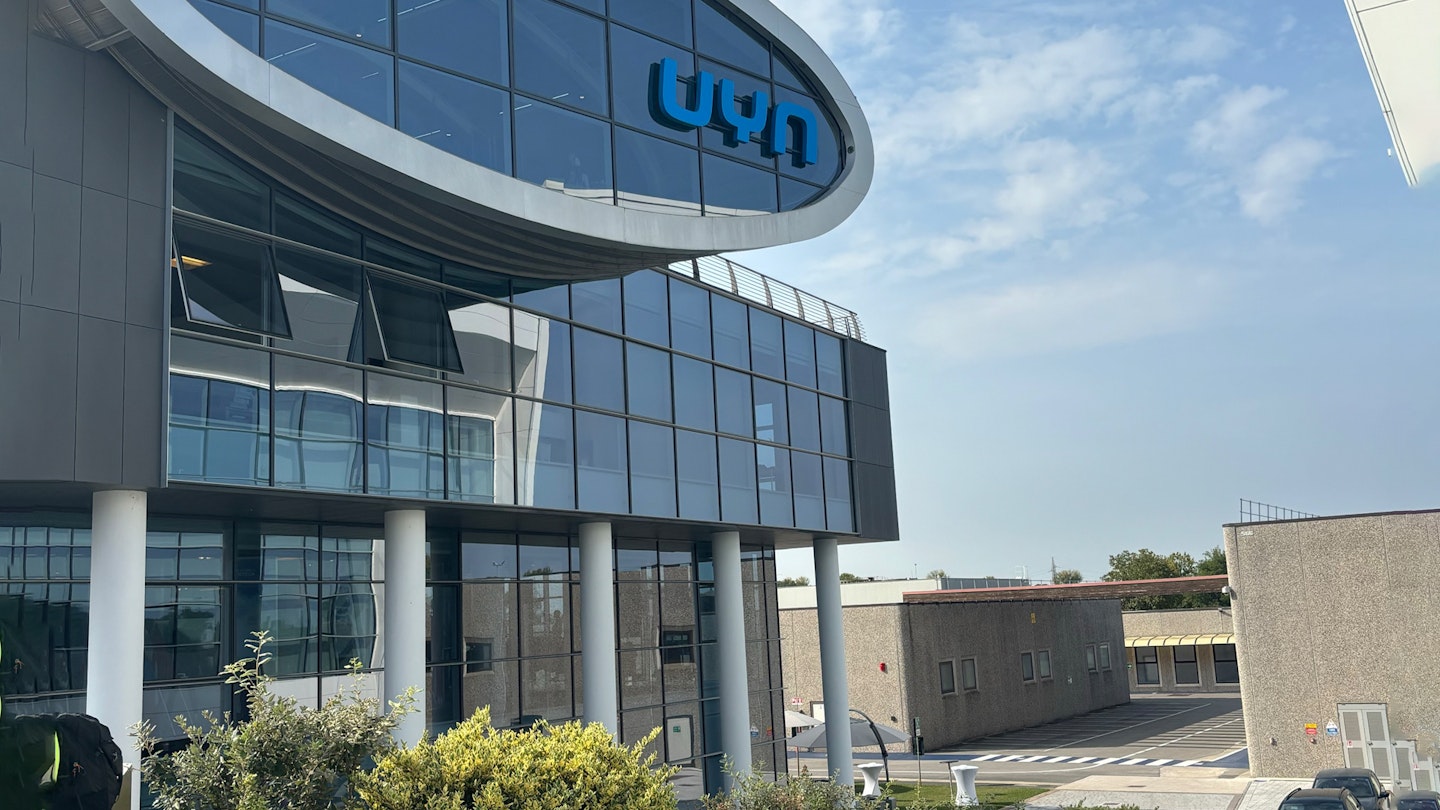
We recently look around UYN's Academy for Research and Engineering in Apparel and Sports, or 'AREAS', for short. We saw their sprawling campus which truly looks like Tony Stark owns it. Their headquarters, design studios, production lines, and top-end testing facility are all in one place.
Because of this, UYN and Trerè have been able to implement systems which solve many of the big wastage problems that often come along with clothing production.
"Synthetic materials are not biodegradable, so it's our responsibility to recycle as much waste as we can, [...] we've reached 100%"
–Mattia Bazzoni, Head of Communications at UYN
UYN produce 14 tonnes of textile waste every year, and they recycle 100% of it. "Synthetic materials are not biodegradable, so it's our responsibility to recycle as much waste as we can," says UYN's head of comms, Mattia Bazzoni, who we caught up with at AREAS.
"And because we have logistics, design, and production all in one place, we have been able to reach 100%.” A large portion of UYN's textile waste is turned into 'Airnest', a lightweight yet dense substance used for insulation in their clothing. Another portion is compressed into insulative panels that Trerè use in everything from car doors in their auto department to the very walls of their HQ.
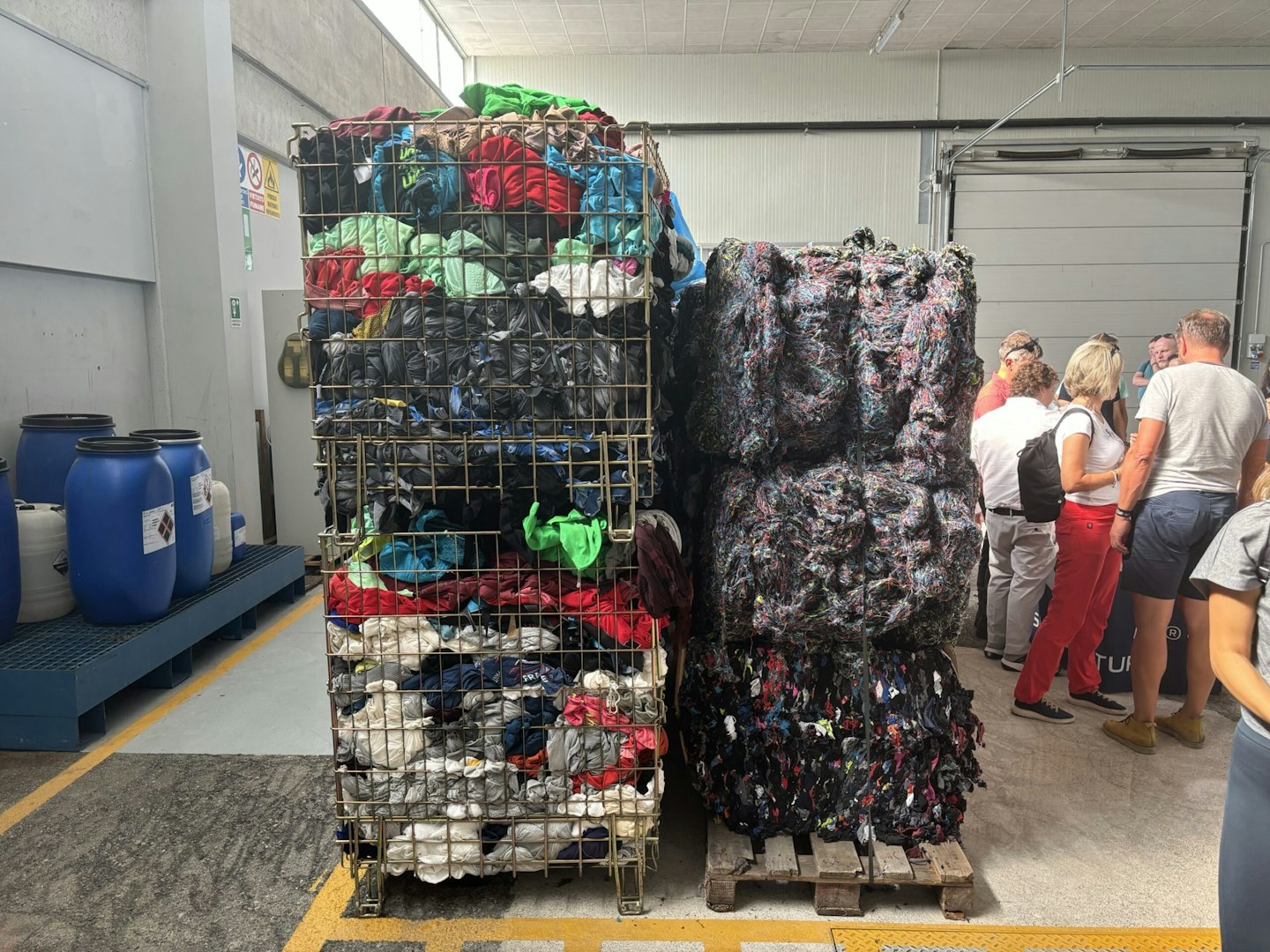
The circular production at UYN is certainly impressive, but the real stars of the show are the materials used in their apparel. UYN's Biotech clothing range is all made from varying combinations of six different fibres. Each fibre comes from a different starting ingredient, each of which is a renewable, natural, and obtained sustainably.
We'll dive deeper into this process in a moment, but first, lets break down the six core fibres that UYN uses, all from natural ingredients.
UYN's signature 6 natural fibres
Kapok
Kapok is, at time of writing, the world's lightest natural fibre. It's a hollow fibre composed of 80% air with a very low density (0.35 grammes per centimetre squared). Due to its extraordinary softness and natural insulating power, Kapok is known as vegetable wool.
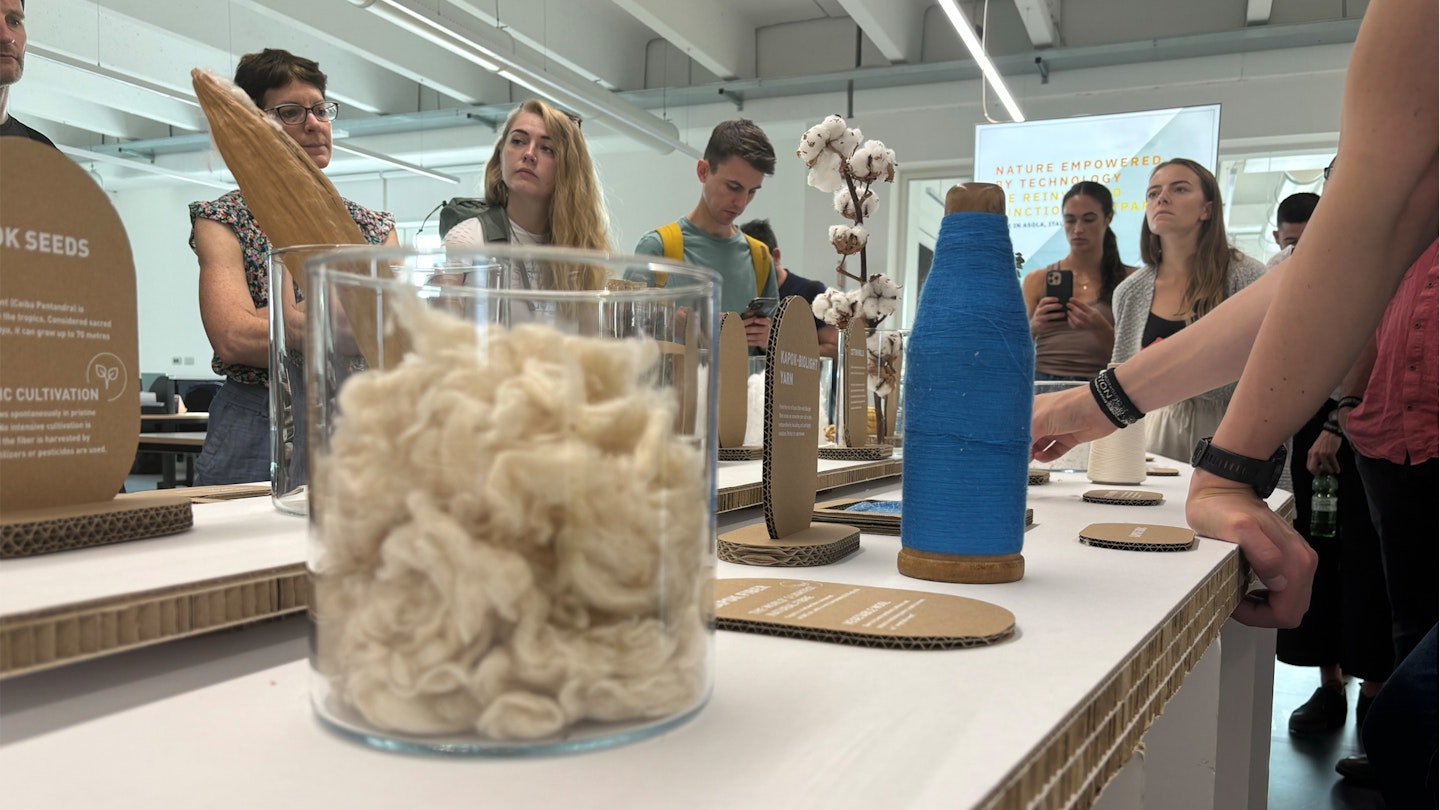
The fibre is harvested by hand in the rainforests of South America. It comes from the fruit of the Ceiba Pentandra, a native plant that is already widespread in the region, so there is no need to aggressively cultivate and farm it.
Natex
Obtained by pressing the seeds of a Castor oil plant, Castor oil is the starting point for creating Natex yarn. Unlike traditional polyamide, Natex is not derived from fossil fuels and has minimal environmental impact.
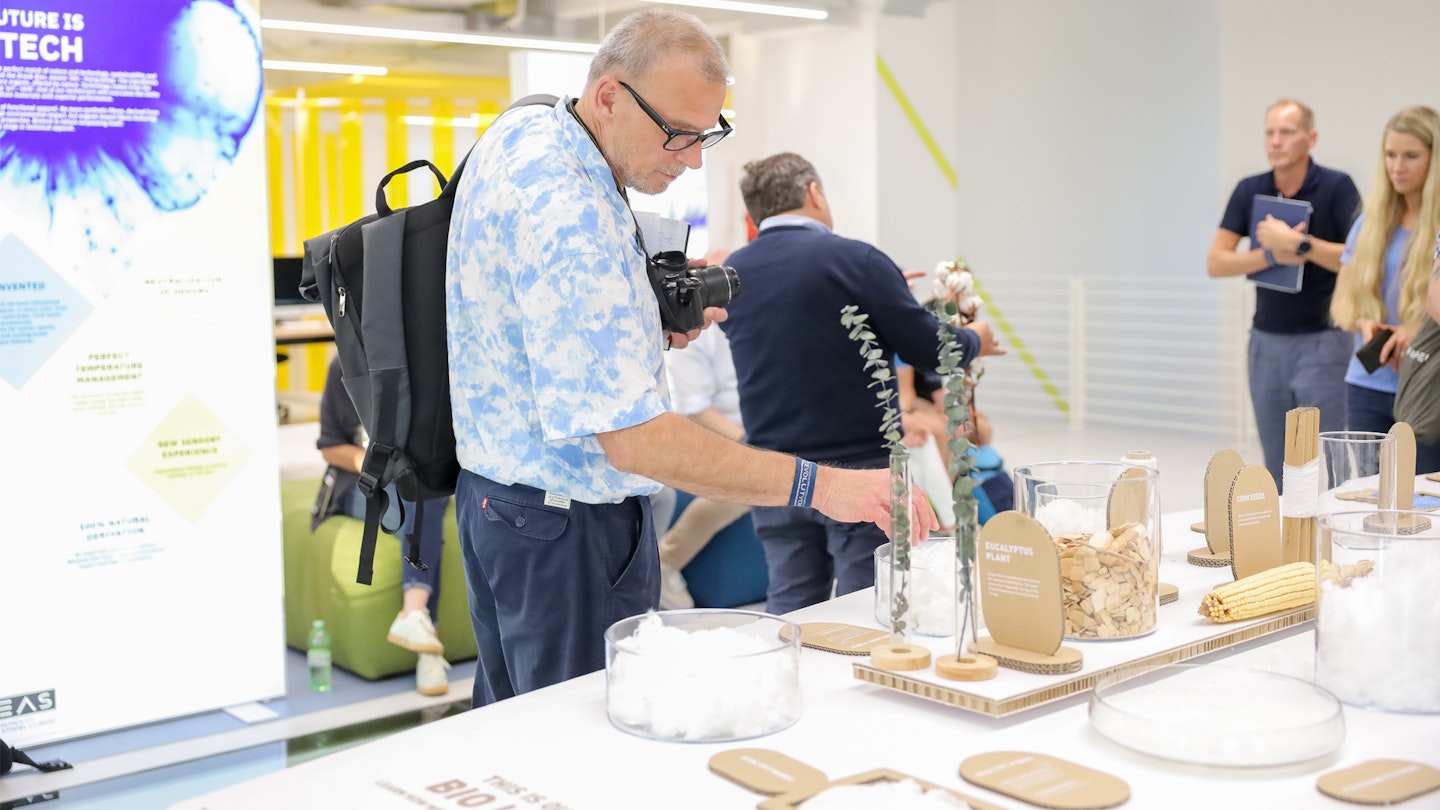
When compared to traditional polyamide, Natex is 25% lighter and 50% faster to dry. It also has a natural antibacterial effect making it anti odour. The castor oil plant generally grows in arid areas not intended for agriculture, therefore it doesn't subtract arable land for food uses.
COOLTH_SL
Cotton is cultivated in more than 90 countries and grown on 2.5% of the world's arable land. The fibre of cotton is obtained from the 'boll' or protective case around the seeds of the plant. But this creates a wasteful bi-product called 'linters', the filaments attached to the seed which are two small to be spun.
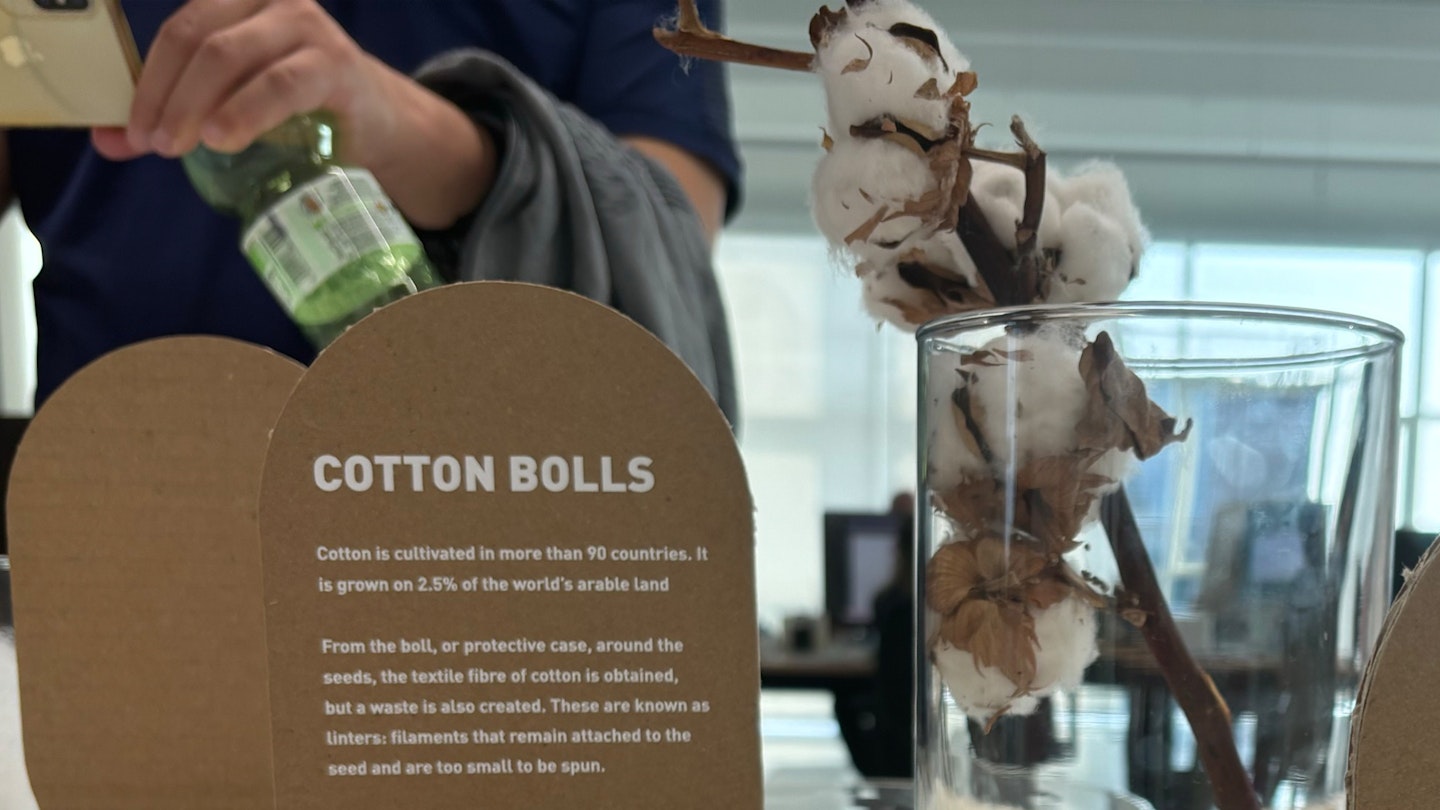
However, it is possible to sustainably process these thin filaments, refining and dissolving them to form a new high performance fibre: COOLTH-SL. This is a hydroscopic fibre that absorbs moisture and keeps your skin cool and dry. It's incredibly smooth, and it returns to nature at the end of its life cycle as it's biodegradable and compostable.
Biolight
Biolight fibre is derived from the cellulose of Beech trees. It's smooth, super soft, and provides an extremely pleasant touch. Like COOLTH_SL, it's also biodegradable.
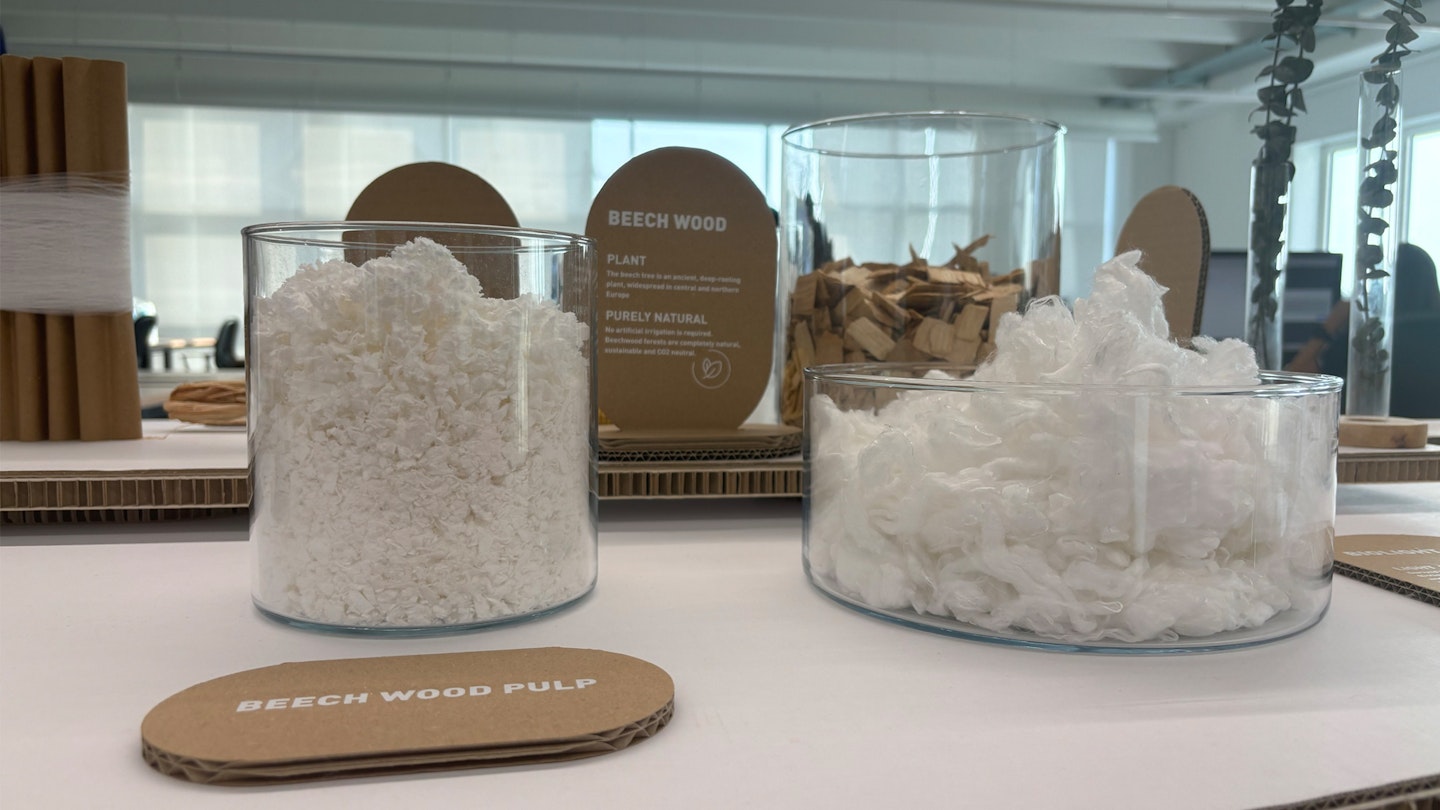
The Beech tree is an ancient deep rooting plant widespread in central and northern Europe. No artificial irrigation is required to grow it. Beechwood forests are completely natural, sustainable, and CO2 neutral. The wood is harvested, chipped, bashed into pulp, then extruded into a ridiculously soft fibre.
Eucalypt
Eucalypt fibre is sustainably derived from the cellulose of Eucalyptus. the wood comes from responsibly managed FSC (forest stewardship council) certified forests.

Thanks to very small hydrophilic fibres, Eucalypt absorbs a large amount of moisture so that it evaporates faster. The fibre is also biodegradable, as UYN put it, it's born from nature and so returns to nature.
Flexicorn
Flexicorn fibre comes from corn seeds that are not used for human consumption and from glucose fermentation. Flexicorn is a sustainable alternative to elastane.
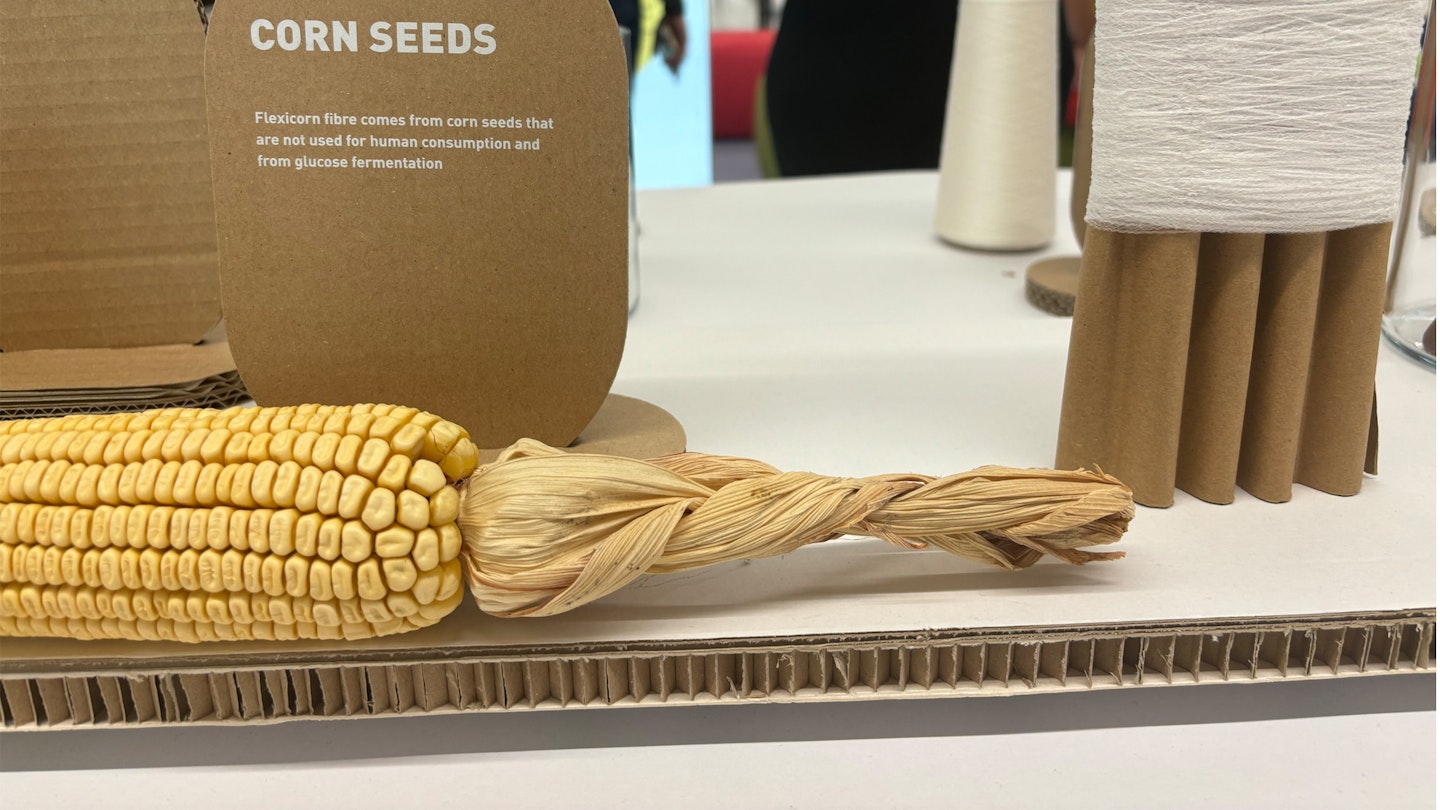
Due to the micro zigzag structure Flexicorn yarn is highly elastic and always bounces back to its original shape. On top of this, it's both wrinkle resistant and UV resistant.
How these fibres are used
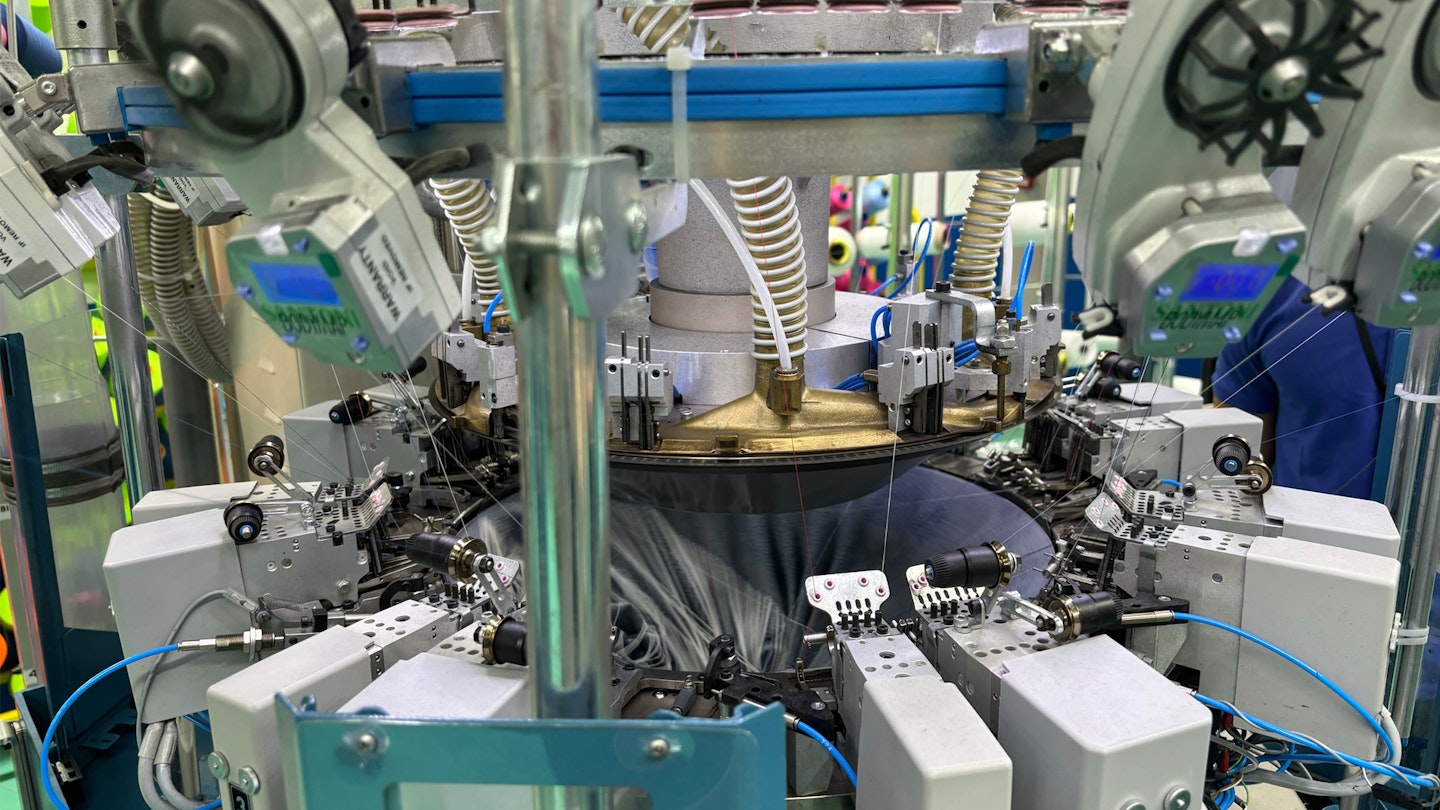
Other companies create clothing with these bio-based materials, "but those are pyjamas, tracksuits, clothes for sitting at home!" says Mattia. "We make sportswear, and we make sure it performs as good or even better than traditional synthetic garments."
The key to UYN's approach is the countless hours they spend blending their fibres to create yarns and innovative sustainable fabrics with the perfect composition for each job. Their clothing can feature yarns with varying percentages of each fibre depending on placement and function.
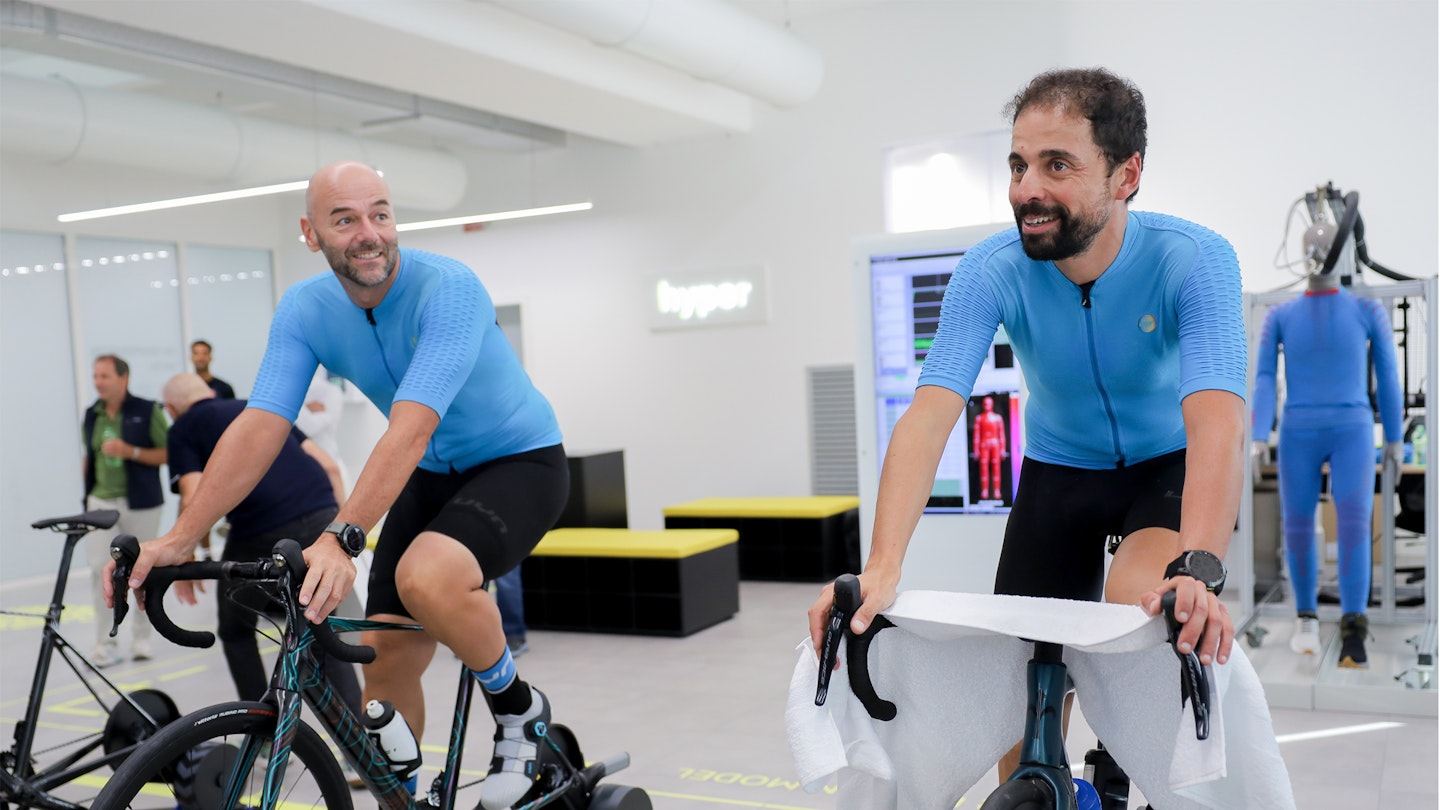
"There's the fabric composition", adds Mattia, "and there's also the way we knit the garments." It's true that UYN's sportswear has tonnes of subtle yet helpful features, like vents on the chest, ribs along shoulders and arms to improve flexibility, and the total omission of seams thanks to some clever design and construction.
"Creating clothing is about having a good recipe and technique" remarks Mattia, sagely, "If I had flour, sugar, eggs, I could make a very basic cake. Maybe. But the best chef in the world could make something far better with the same ingredients. The way we engineer the fibres, how we combine them, where we place them in the garment, that's what makes us special."
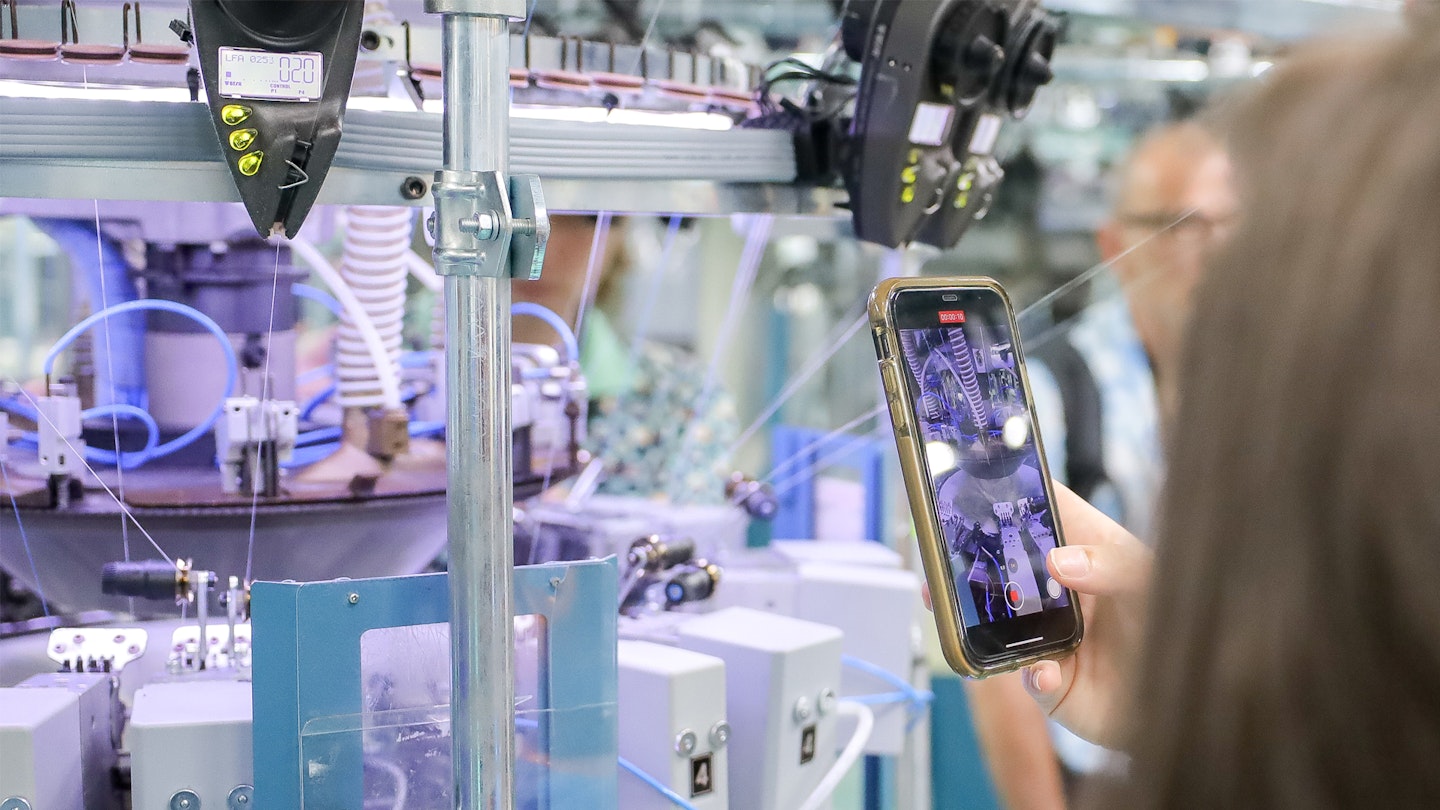
"We need to find something to replace crude oil", this is the primary thrust of UYN, "to replace petroleum in clothing. It's that simple. And we have, we use the glucose in corn, the oil from castor beans, wood from different trees. Every fibre starts with a renewable ingredient."
On top of their use of bio-materials, UYN also washes every garment with a filtration system which helps them to reduce the amount of microplastics in the fabric. “Whenever you put synthetic material in a washing machine, they will release small particles into the water. But our filtration system catches the released microplastics, and we recycle them into, for example, insulated panels for buildings and cars.” Say’s Mattia. “In one day, we are able to trap 425,000 microplastics, which, if you lined them up each next to each other, would be 382km in length.”
"That's the distance between Asola and Munich"
–Mattia Bazzoni, Head of Communications at UYN
“We also use a treatment on each yarn, and a particular way of knitting the fibres to prevent the release of microplastics. This also makes the garments more durable and prevents pilling.” Pilling is the mortal enemy of every synthetic garment.
UYN prevent pilling in three ways. The initial treatment of the yarns, the combination of various fabrics throughout each garment, and their signature style of tight knitting which avoids any stitched seams or loose threads. We got a look at the machines that weave these garments together, and they are pretty darn heavy duty.
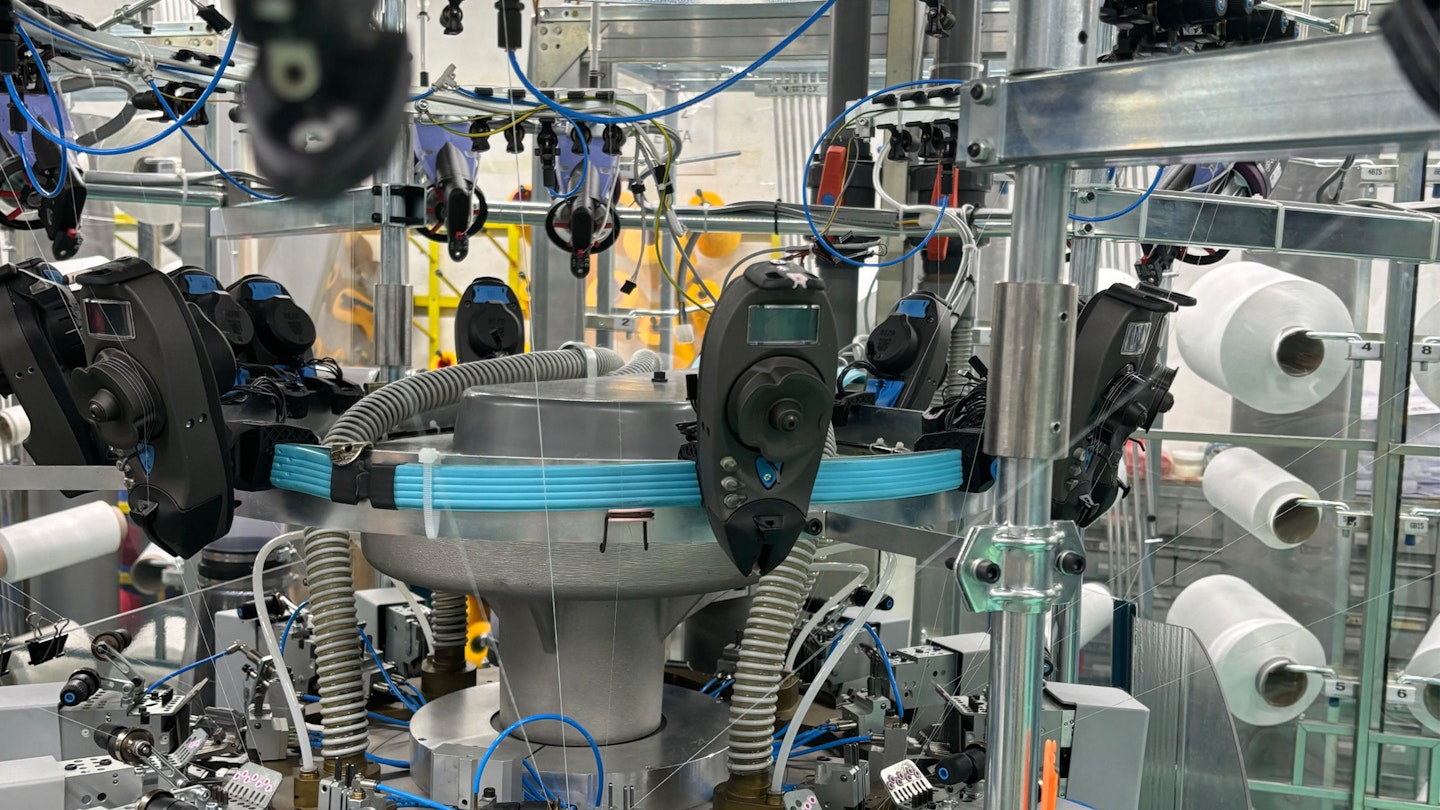
"For the clothing, we select the fibres according to performance, and environmental impact. For example, castor oil seeds, the plant is not used for human consumption and grows spontaneously, so it doesn’t affect the economy or food networks. Therefore, we can afford to use it in high quantities.
"But corn seeds, growing corn seeds has more environmental impact that castor seeds. So we use Flexycorn in a smaller percentage. It’s a balance that we constantly aim for, but ultimately, we do put performance first.
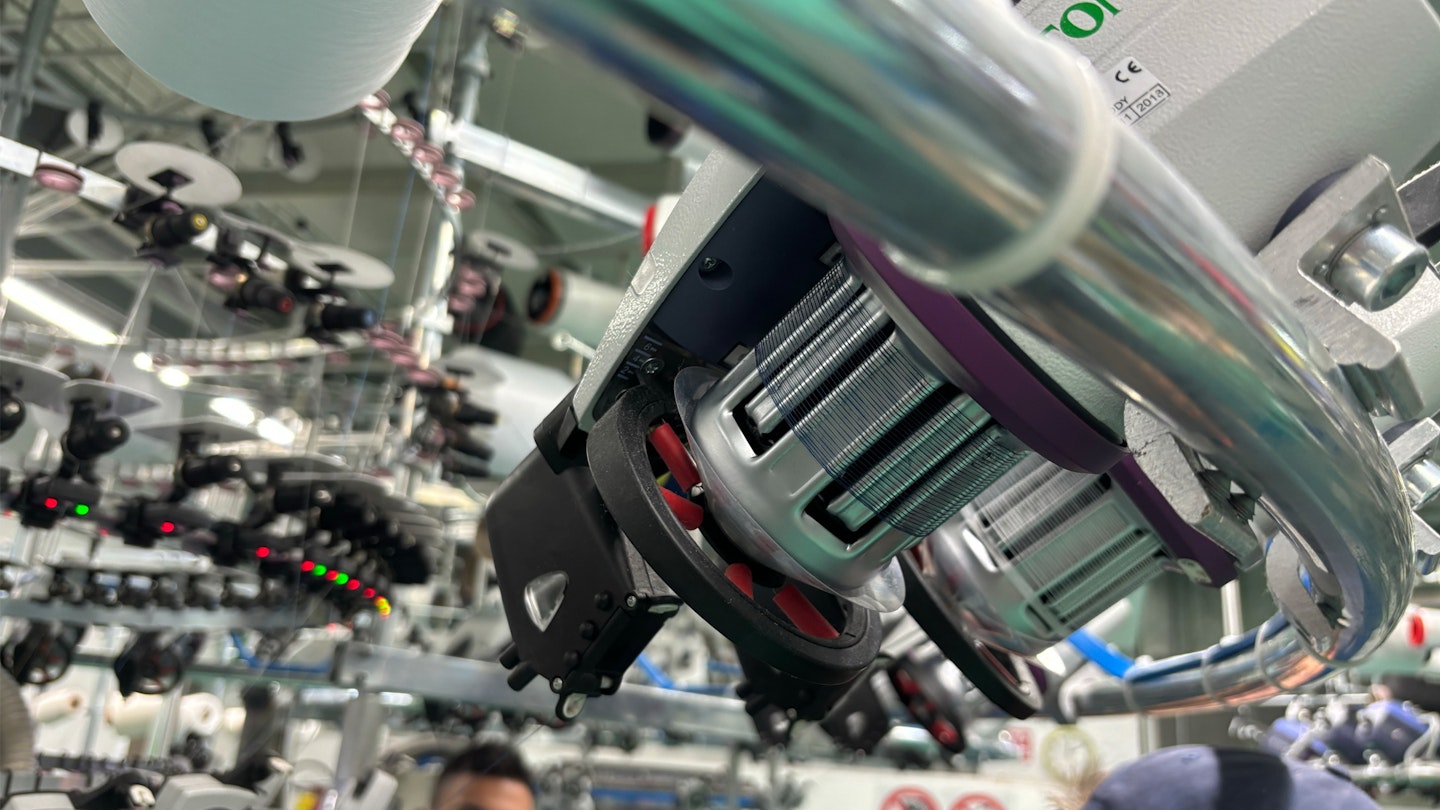
“For example, our underwear are 99% bio based because we use traditional elastane in the waistband. It’s better to get the perfect fit, and we can afford to spend that 1% to get there”.
It’s remarkable to hear this admitted as though they fell short, when the percentage of bio-based materials in most outdoor clothing and sportswear is a big fat zero. That said, we are seeing some progress in other brands, with the Allbirds Trail Runner SWT being a shining example of a bio-based trail running shoe. But there's still far more work to be done.
We’re thoroughly impressed by the circular and sustainable practices that UYN and Trerè have demonstrated, and we’re hoping more companies follow suit.
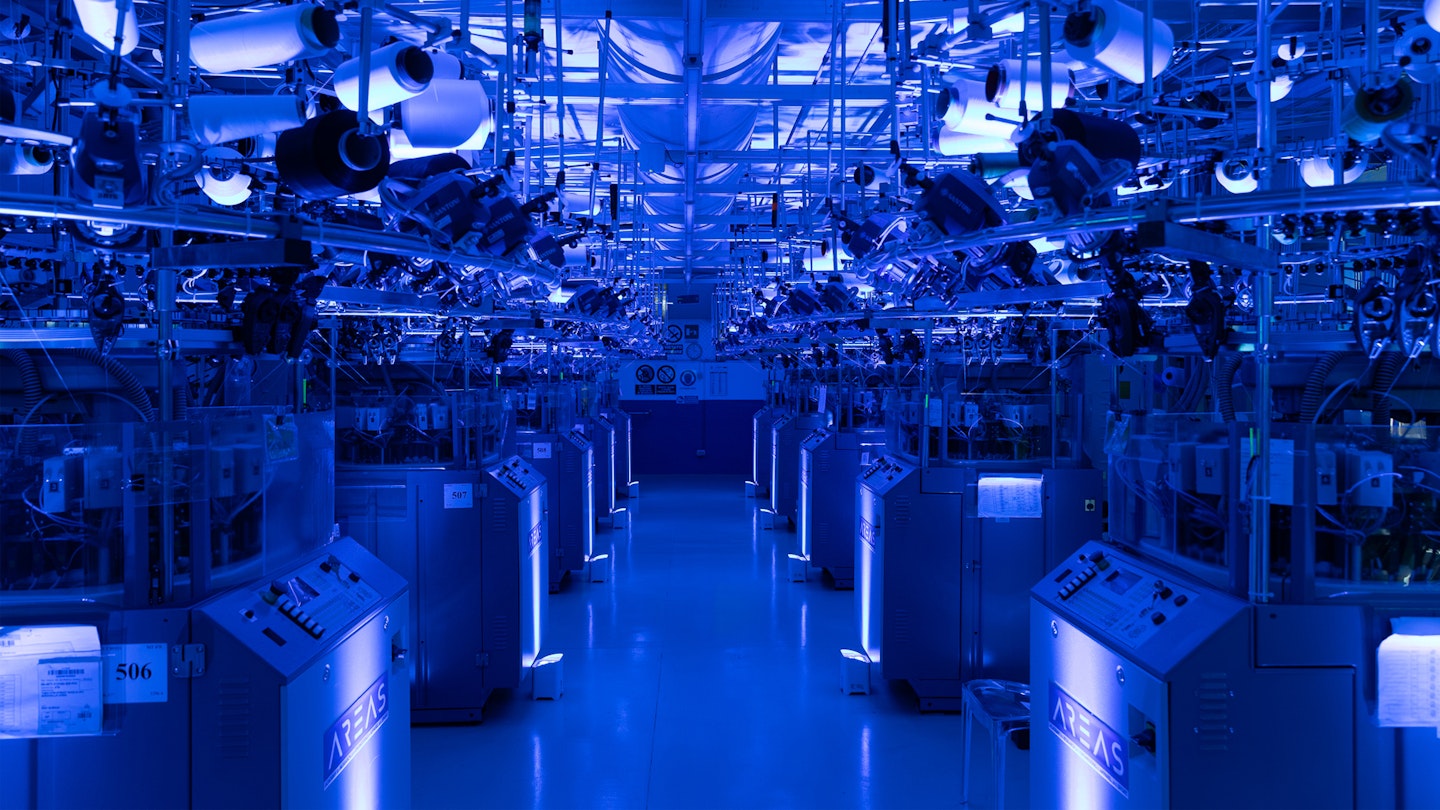